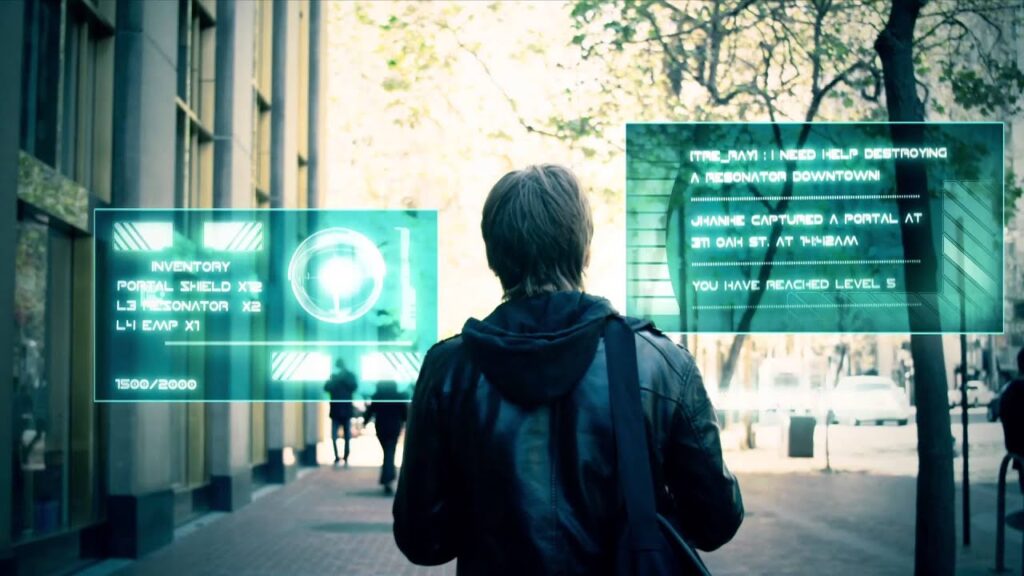
London sex chat rooms are a place in which people of both the sexes interact to talk about sex. The best part of this is that you can do it at any time of the day or night – even while watching television! You will never get a more candid opinion or a frank discussion than what you will get in these rooms. The chats are conducted by experts and experienced users with great insight into the bedroom behaviour of both genders.
You might think that chatting online is shameful or unsavory. In fact, this form of communicating is increasing day by day. There are a lot of places where you can go to on the internet to chat to people. However, London sex chat rooms are discreet and private. This means that your discussions and responses remain confidential and will not be shared with anyone else on the site.
Some of the biggest sites for chatting have hundreds of thousands of members. Most of these chat rooms are separated by gender. This makes it easy for couples, gay or straight, to find a partner. Chatting online with women in London is an extremely popular activity.
There are a large number of reasons why women would use these chat rooms. Some women just want to have a good time and have fun. They enjoy sharing and discussing with like minded people. Many women like to chat with strangers as it makes them feel more relaxed and confident. When you chat with strangers, you are often put on a bit of a trial and error basis as you will not know whether you are dealing with a genuine person or someone of a different identity.
There are many advantages to chatting online with women. Although women may sometimes feel uncomfortable and even a little embarrassed about talking to members of the opposite sex, they will usually be surprised how comfortable and helpful chatting with members of the opposite sex can be. The majority of women who frequent chat rooms for sex also admit that their favorite pastime is getting to know new people. This means that if you are a single man or a married man looking for a date, you may find chatting in one of these chat rooms very helpful.
You should be aware that you may run into women who are fake. This does happen on the Internet and you have to be careful. It is often the case that there are women out there who pretend to be interested in dating men but really want only to meet up with their friends. However, there are chat rooms which have several genuine members looking for a date or a sexual relationship.
Adult text chat
For those who are sexually inexperienced, one of the best ways to learn about how to make love to someone is through adult text chat. Adult text chat has indeed evolved as an interactive way to have fun and discover new things, especially for those people who are adventurous. And because of its increasing popularity today, you will be able to find countless number of people using it to discover more and to satisfy their needs and desires. Here are some of the basic things that you need to know about text chat operators:
- You can make money through adult text chat operators. This is quite a common question. In fact, this is also one of the most frequent questions that people ask if they are interested in starting up an online business or a service like that. You can be as successful as you want if you will be working from home.
- English is not a necessity for being a text chat operator. You don’t really need to have a great amount of experience in this kind of field. All you need to have is a good grasp of the written English language. Most of the employers of such services usually require you to have at least a basic understanding of the written English language.
- Most adult text chat operators usually prefer to work with people who are native English speakers. Most of them actually prefer working with people who can speak and understand the English language. Of course, you should have a thorough understanding of the English language yourself. Aside from that, you must also possess basic knowledge on using the English language on chatting. By knowing these two important things, you will surely be able to communicate effectively with your fellow clients.
- In addition to that, you should also be open to trying new things in order to maximize your earnings through your online business ventures. There are lots of opportunities for you to enhance your skills and knowledge in the world of online chatting. Some of the things you can try include including creative typing style in your ads or creating avatars in your chat rooms. In fact, you will never run out of options when it comes to enhancing your skills in availing the different kinds of interactive features that are commonly offered by many adult chat rooms.
- Be wary of your privacy settings while participating in online chat rooms. You should never reveal personal information like your address, age, or your location through your online chatting activity. You must take extra precaution to avoid your IP address to be traced. This means you must either change your IP address whenever you wish to participate in any online chatting activity or else choose to remain anonymous. This way, you will be able to enjoy your chats without worrying about your privacy.
Strip chat
What is strip chat? It’s a fun new way for people to explore their sexuality and to find people of like-minds on the Internet. If you’ve ever seen an “adult video” on television, you may have noticed that they are often filled with “stripping” or “striptime”. The term “strip” comes from the fact that stripping is often a part of the act of lovemaking. But in today’s world, strip chat is becoming a popular method for exploring one’s erotic side – and perhaps even of passing a sort of moral judgment on one’s partner.
How is stripchat different from regular webcam sex? Well, stripchat allows its users to express themselves as naked or nearly naked. They can “strip for real” on a website that offers a paid membership. When someone decides to strip chat, that person actually removes all clothing except for their webcam and begins to make their sexual moves on another person. Usually, though not always, the webcam is switched off.
Can I see live sex chat on my computer? Many people new to strip chat are usually a bit shocked to find out that it actually works. Live sex cams can be found on several different websites. Some of them include actual live webcams, which will allow you to actually watch the person doing the “striptime” on your computer – meaning you’ll get some real time feedback on how they’re doing. Other websites feature a variety of visual “cams” that look a bit like mini PowerPoint presentations, and which you can either view live or save to your hard drive for later.
Do I need to pay to use live webcam sex shows? There is usually no charge to view live sex cams on websites that offer adult content. However, there are often some membership fees for websites that feature more sophisticated types of cameras (like IP cams). You can generally find websites that offer a one time, low fee, monthly plan that will allow unlimited viewing of various types of cams.
Are there any advantages to using “strip club” style tokens? Actually, there are a few advantages. First of all, since you’re in a public chat room, you have to deal with other users who may not share the same interests as you do. If there’s no one to show up to your cam show, it’s not going to help your search for new friends. Also, if you don’t know anyone in particular through this “stripper” chat option, you won’t necessarily run into any “strippers” at all. However, many women do talk to others in these public rooms and finding someone with similar interests is usually quite simple.
Can I get more tokens for “private shows”? Yes! As I said before, you can buy an unlimited amount of strip token credits from some online cam sites. For each additional token you purchase, your choice of private show duration increases. You can have up to 30 minutes of private time on one of these sites for just a few dollars per month!
London striptease girls
Gay video chat
Gay video chat rooms have taken the internet by storm. People of like mind to use these chat rooms for their own special purposes. Whether you are looking to hook up with a gay man or woman, or are just a big fan of the gay community, you too can join in the fun. There is no need to be ashamed about your sexuality, because the people in the gay online chat rooms are like minded and won’t judge you.
Gay online chat rooms are a special section that caters mainly to curious and gay men who wish to meet gay men in public. The popularity of these rooms has soared in the past few years. There are literally thousands of gay men worldwide using the Funyo gay video chat from all different backgrounds, nationalities, and sexual orientations. In many cases they do not even have to talk face to face, as the software makes it possible for them to get right in there with other members. No more shyness from most gay men either, they are extremely open and comfortable with their sexuality.
For those men who wish to try out a new experience, you can always consider signing up for a gay chat room. There are always fresh and active gay guys available for a date, friendship, or even sex. With a free gay chat room you get to interact with like minded gay men all over the world.
The best part about using a gay video chat platform to make new friends is that it is free. There is no cost to use the service and you don’t have to spend any money to be able to access it. You will only need an internet connection to log on and start meeting new friends that share your same interests as you. This free gay online chat platform also allows for free photo uploads, so if you ever decide to meet new people, you can show off your best attributes.
A few of the other free gay video chat features include an image chat, gay video chat features, voice chat and many more. You get to communicate with another member as if you were actually sitting next to them in real life. You can easily identify certain characteristics of the other person, based on how you think he/she may be acting. It is a great way to develop an instant connection with someone, who shares the same interests as you.
Chat rooms for gay men are often overlooked when it comes to meeting people who are located anywhere in the world. The ease of which you can get connected with another gay man is just an added advantage, without registration, you could easily be connected with someone in 20 minutes. If you have never used this feature before, you should definitely give it a try. Even if you haven’t used gay chat rooms before, it’s never too late to try them out. All you need is an internet connection, which is almost always available, and then you’re ready to start chatting!
Sex chat bot
Nowadays, sex chat bots are becoming a normal occurrence in online society. In fact, some even use sexting software and chat simulator tools to improve their vernacular. Some may even meet their sexual dreams through a sex chat bot. These bot systems allow people to live out their most fantasy-playing sexual fantasies by simply interacting with a sex bot. However, despite the wild popularity of sex chat bot systems, there are still some people who are not aware of these naughty bots. Thus, this article will be explaining to those uninitiated what a sex chat bot is and what it can do for you!
Basically, these types of chat Bots are programmed to interact with users in an interactive sexual environment. Unlike regular human communication strategies, such as writing in all caps or spelling words incorrectly, sex chat bots work with natural language processing. This allows the user to have a more personal conversation with the bot, which can result to a more intimate and descriptive conversation. What’s more is that the interaction is mostly between the two people, and not between the artificial intelligence system of the bot as is often the case with other chat bots. For instance, some sex chat bots work with voice commands that allow the user to talk to the bot like he or she would to another human.
Many sex chat bot systems also use simulators. Using these simulators, a person can increase his or her self-esteem. In fact, many teenagers use these simulators to feel more confident about themselves. As a matter of fact, many schools now use sex chat bots as a way to boost their student’s self-esteem. In fact, there have been several scientific researches done on how simulators affect different people in different situations.
Sex chat bots are also used as a means of relieving stress. For instance, one bot, called Boobs, relieves a user of his or her worries after being on a date. It is like talking to the bot, and it even interprets what is said by the user and uses it to gauge the situation and its outcome. There are even sex chat bots that use complex algorithms to calculate and predict what will happen in a certain situation, much like a stock picker robot.
Another use for sex chat bots is in the arena of seating styles. These are married couples who want to practice safe sexting styles. The married couple uses a sex bot, calledbottr, to practice sending messages to each other, without revealing any identifying information. There are some drawbacks to this method, however.
Since there is no way to see the expressions on the person’s face, or how he or she is responding to the situation, there is a chance that the messages that the bot sends could be misinterpreted by a partner. However, there are also many benefits. For instance, people who want to flirt would rather engage in this activity with a sex chat bot, rather than an actual human partner. Also, since the bot only responds to certain messages and cues, it eliminates the possibility of misunderstandings. The bot is also a great learning tool for those who want to practice reading body language or signs of attraction in real people but are not comfortable talking up a stranger.